1.目的
確保生產制程、產品入庫及出貨均在有效管制狀態下執行,從而使出貨產品質量符合客戶要求。
2.適用范圍
本文件適用于原材料投產到成品出貨之間各個環節的品質管控。
3.參考文件
無
4.定義 Definition
PDCS:Process Defect Contact Sheet 《制程異常連絡單》.
QIT:Quality Improvement Team 品質改善小組
PDT:Production Design Team 產品開發小組
5. 職責 Responsibility
5.1. QE Quality Engineer
5.1.1.負責PFMEA、Control Plan、檢驗規范(SIP)等文件的制定.
5.1.2.負責異常責任單位的判定及產出品處理方式的確認.
5.1.3.負責制程參數優化時的評估和質量確認.
5.1.4.負責量試產品處理方式的確認,協助生產單位和工程完成各項改善.
5.1.5.負責量試產品問題點的匯總并分發各單位.
5.2 品管 Quality controller
5.2.1.負責依據檢驗規范對產品進行各項質量決議和查核.
5.2.2.負責制程巡檢出現異常時制程異常聯絡單的開立及產品改善和處理結果的確認.
5.2.3.負責制程參數優化時相關變更紀錄的確認和產品質量的監控.
5.3 工程 Manufacturing engineer
5.3.1.負責制造作業規范,包裝作業規范等文件的制定.
5.3.2.負責制程異常的分析,處理和完成相關驗證.
5.3.3.負責制程參數優化時的評估,驗證和SOP的修訂.
5.3.4.負責主導量試產品問題點的檢討和改善措施的提出.
5.4 生產單位 Manufacturing dept.
5.4.1.負責按各項要求執行生產.
5.4.2.負責制程參數變更時的記錄和跟催確認.
5.4.3.負責各項改善計劃或措施的完成.
6. 作業程序
6.1 產品質量計劃制定及應用
6.1.1 產品質量計劃架構
產品質量計劃包括FMEA、Control Plan、檢驗規范(規格)(SIP)、制造作業規范(SOP)等文件.
6.1.2 DQE于新產品量產前制定FMEA、Control Plan, 并召集制造等相關單位檢討.
6.1.3 制造作業規范制定
制造作業規范由工程科制定, 內容包括使用材料、使用設備、作業條件、作業步驟及作業自主檢查等,作業規范應配合圖面或圖片來說明, 使作業人員更易了解.
6.1.4 檢驗規范制定
檢驗規范由QE制定, 內容包括抽樣計劃、檢驗方法、檢驗規格、檢驗設備、檢驗表格、判定標準及管制措施等.
6.1.5 應用管制
各制造部門應指派人員負責管理FMEA、Control Plan、制造作業規范、檢驗規范等, 確保作業現場所使用或所懸掛之文件為最新版本.
6.2初件檢查
生產單位于每次開機、開線、設備維修、換料、更換機臺或線別時, 抽取首件,線長在確認外觀OK后,填寫《初件檢驗記錄表》送交IPQC, IPQC依SIP、圖面、簽樣等實施初件檢查, 并將結果記錄于《初件檢驗記錄表》. 無法立即完成之檢驗項目, IPQC可暫時判定合格, 此項目若最終判定不合格, 需及時追溯并知會生產單位進行改善, 問題嚴重時需開出《制程異常連絡單》.
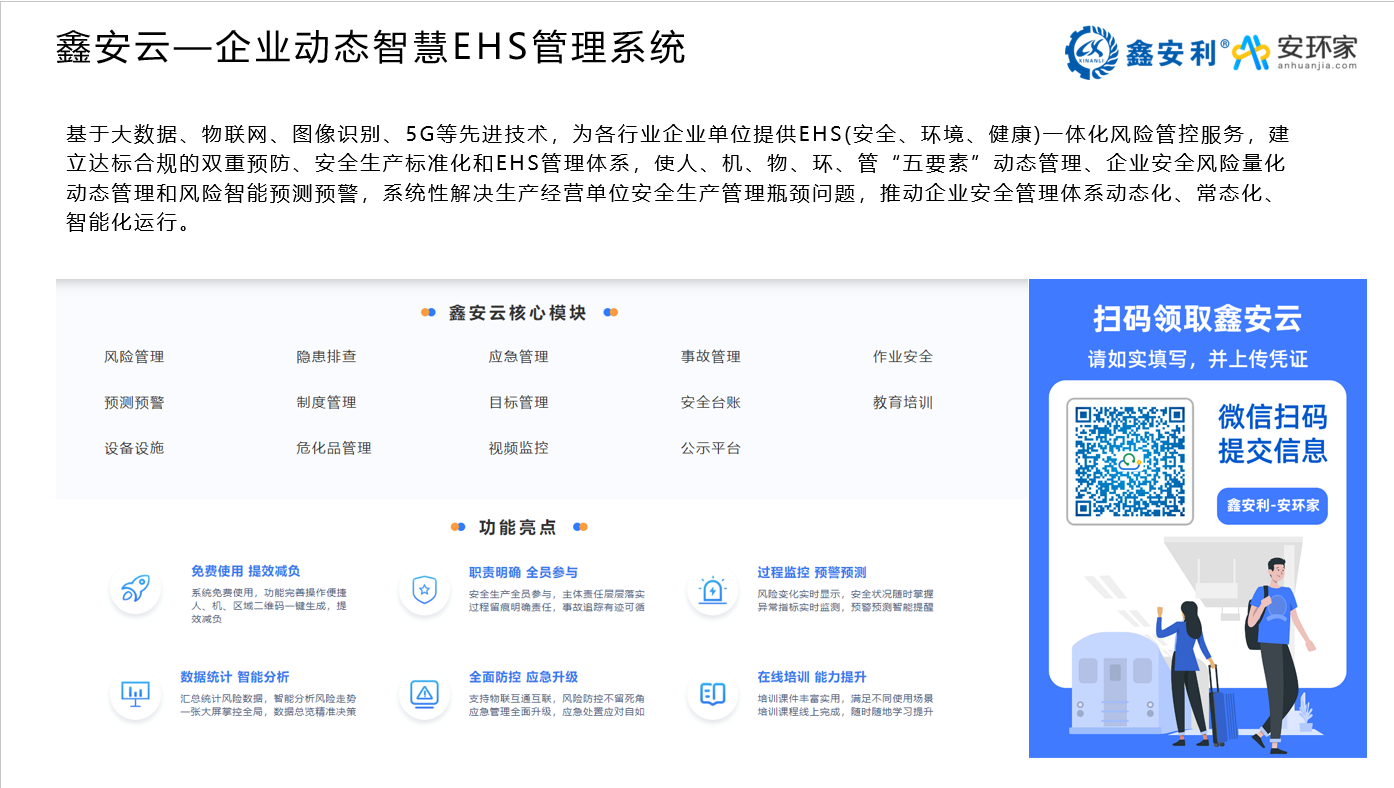